10 Best Software Used by Mechanical Engineers in 2025
- UPES Editorial Team
- Published 15/07/2025
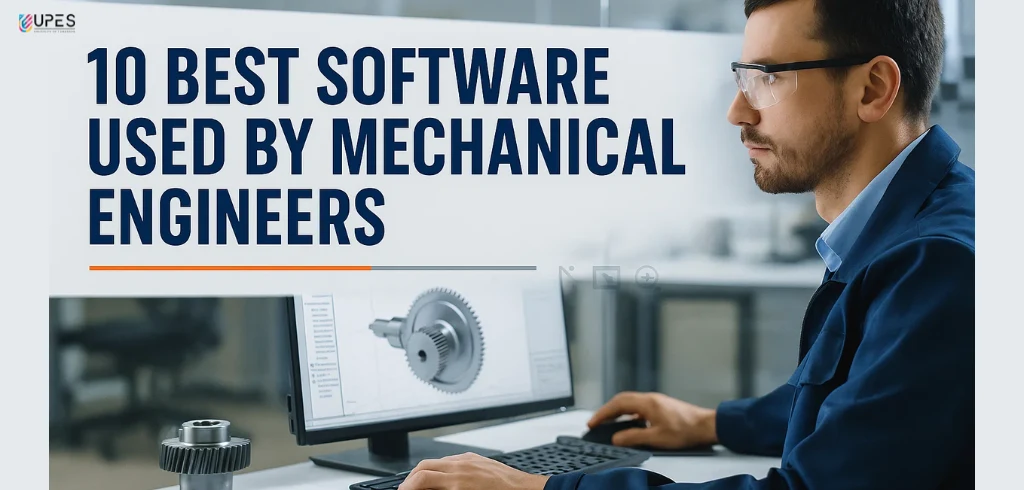
As mechanical engineers you would be expected to have a mastery over design, analysis, and manufacturing. With technological advancements, it is natural to experience an increased reliance on mechanical engineering software that enhances work productivity and righteousness.
Become future-ready with our Advanced Engineering programs
Know MoreHere’s a blog to help you understand the variety of mechanical engineering software available to help you ace at your job or course. These tools act as doorway to modern mechanical innovation and a mastery over them will help you try hands and conquer the fields of product design, thermal analysis, robotics, and advanced manufacturing.
10 Best Software Used by Mechanical Engineers in 2025
Listed below are the top ten mechanical engineering software both students and professionals should master for the enhanced knowledge, skillset, and career upliftment. Have a look:
1. AutoCAD
AutoCAD by Autodesk is one of the earliest computer-aided design tools developed for engineers. It is primarily used for 2D drafting, schematics, and layout design, offering accuracy and standardization in engineering drawings. AutoCAD works best when used to manufacture blueprints, assembly layouts, and piping diagrams.
- Purpose: 2D Drafting and Drawing
- How to Use: Engineers begin with basic commands like line, circle, offset, and dimensioning to draft precise components. Layer management and block creation enhance drawing organization and reuse.
- How to Master: Proficiency comes with regular practice of drawing exercises and understanding dimensioning standards. Different careers in mechanical engineering will demand knowledge of different type of software. Make sure to master AutoCAD and others.
2. SolidWorks
SolidWorks sits at the intersection of design creativity and mechanical simulation. This CAD software is highly regarded for its 3D modeling and product development capabilities.
- Purpose: 3D CAD Modeling and Simulation
- SolidWorks is widely used to model parts, simulate mechanisms, and validate designs using stress analysis and motion simulation. It is popular in industries such as consumer products, automotive, and medical devices for rapid prototyping and assembly design.
- How to Use: Start by creating 2D sketches, extruding them into 3D bodies, and applying features like fillets and shells. Simulations for stress and thermal effects can be conducted using the integrated SimulationXpress tool.
- How to Master: Mastery involves project-based learning—modeling real-life components and running simulations on them. Tutorials from Dassault Systèmes and structured academic modules such as those offered in the Mechanical Engineering program at UPES are ideal entry points.
3. ANSYS
As mechanical problems grow in complexity, simulation software becomes indispensable. ANSYS leads in solving problems related to structural mechanics and thermal effects.
ANSYS enables engineers to simulate stress, strain, vibration, and heat transfer in mechanical components. The software is essential in industries that demand high-performance and reliability—such as aerospace and heavy machinery.
- Purpose: Finite Element Analysis (FEA)
- How to Use: Engineers import CAD models into ANSYS, apply material properties, boundary conditions, and mesh settings before solving the system. Results are visualized as stress contours, deflection maps, and fatigue life predictions.
- How to Master: Understanding solid mechanics and meshing principles is critical. Start with basic static structural problems and move toward complex coupled-field analyses. Complement this knowledge with academic projects that integrate simulation tools, helping bridge the gap between theory and practice. For career alignment, read more about mechanical engineering pathways.
4. CATIA
Mechanical engineers often encounter highly complex surfaces and assemblies. CATIA is designed to handle such sophistication with ease.
Developed by Dassault Systèmes, CATIA is used extensively in aerospace and automotive industries. It supports a full suite of design, analysis, and manufacturing applications, including surface modeling and sheet metal design.
- Purpose: CAD, CAM, and CAE for Complex Systems
- How to Use: After defining the workbench (Part Design, Assembly Design, Generative Shape Design), users can create parametric models and run motion simulations. CATIA’s integration with PLM systems allows design teams to collaborate efficiently.
- How to Master: Start with Part Design and build toward complex assemblies. Mastering surface modeling and generative design is key. Academic programs often incorporate CATIA into workshops and coursework, providing early exposure to industry workflows.
5. MATLAB
Engineers who rely on data, algorithms, and simulations find MATLAB indispensable. It serves as a robust analytical tool across academic and industry applications.
MATLAB allows mechanical engineers to perform complex numerical calculations, create control systems, and analyze large data sets, helping shape their career outcomes. It is particularly useful in research, robotics, and automation.
- Purpose: Numerical Computation and Control System Design
- How to Use: Users write scripts in the MATLAB environment to solve equations, run simulations, and visualize data. Toolboxes like Simulink are used for modeling dynamic systems.
- How to Master: Familiarize yourself with MATLAB syntax and linear algebra concepts. Solving small automation or vibration problems helps build confidence. UPES offers hands-on lab experiences that connect such tools with real-world problems.
6. PTC Creo
Formerly known as Pro/ENGINEER, Creo is a strong contender in product design for its versatility and performance.
Creo is ideal for modeling parts and assemblies, performing thermal and structural simulations, and generating CAM data for CNC machines. Its parametric design approach allows real-time design changes.
- Purpose: Parametric 3D Design and Simulation
- How to Use: Users build sketches, apply constraints, and extrude them into 3D models. Assemblies can be tested for interferences, and simulation modules assess durability.
- How to Master: Practice with complex assemblies, learn geometric dimensioning and tolerancing, and explore Creo’s generative design features. Academic institutes often provide Creo licenses for learning through design labs.
7. Fusion 360
The future of engineering collaboration lies in the cloud. Fusion 360 enables cloud-native design workflows for faster and smarter engineering.
Fusion 360 combines modeling, simulation, and manufacturing in a unified platform. Engineers appreciate its real-time collaboration capabilities and intuitive interface.
- Purpose: Integrated CAD, CAM, and CAE on the Cloud
- How to Use: You can create sketches, 3D models, and assemblies, then simulate stress, modal, and thermal effects—all in the same workspace. CAM modules help generate G-code for 3D printing or CNC operations.
- How to Master: Work on small product design projects. Use Fusion’s community resources and tutorials. The tool is particularly useful for startups, entrepreneurs, and students looking to validate concepts quickly.
8. COMSOL Multiphysics
As interdisciplinary design becomes the norm, tools like COMSOL that simulate multiple physical domains are gaining importance.
COMSOL enables simulation of coupled systems—fluid dynamics, structural analysis, electromagnetics—making it a powerful research tool.
- Purpose: Multiphysics Simulation and Modeling
- How to Use: Begin by defining geometry and physics, set up the solver configurations, and analyze results via parametric sweeps or time-dependent solutions.
- How to Master: Gain foundational knowledge in each physical domain and gradually integrate them into coupled simulations. Exposure during research-based internships or thesis projects enhances comprehension.
9. Revit (for MEP)
Mechanical engineers involved in HVAC, fire safety, and plumbing systems increasingly rely on Revit for accurate MEP design.
Revit supports Building Information Modeling (BIM) for integrated mechanical design. It ensures error-free layouts and coordinated construction documents.
- Purpose: BIM for Mechanical, Electrical, and Plumbing
- How to Use: Create duct, pipe, and HVAC layouts with parametric families. Use clash detection to resolve design issues early in the process.
- How to Master: Understanding HVAC principles and architectural design helps. Practical exposure through lab work or internships in the construction sector is beneficial.
10. Autodesk Inventor
Inventor blends powerful modeling tools with mechanical simulations, offering an alternative to SolidWorks and Creo.
Inventor is suited for machine design, mold design, and motion simulation. It supports parametric modeling and is integrated with AutoCAD for drafting.
- Purpose: Mechanical Design, Assembly Modeling, and Simulation
- How to Use: Build parts, assemble them, and apply constraints. Use stress analysis or animate mechanical systems for validation.
- How to Master: Hands-on modeling of real-world machinery—like gear trains or hydraulic components—can speed up learning. Many mechanical engineering curricula now include Inventor in elective modules or design projects.

Our counsellors are just a click away.
Final Word
A fluency in technical skills like simulation, 3D modeling, or control systems, and more can be very useful to launch your career to great heights as mechanical engineers. Learning of mechanical engineering software pave the way for a brighter future that’s capable of carving a niche in research, manufacturing, design, and automation.
To build a strong foundation in such tools and align your learning with industry needs, explore the B.Tech in Mechanical Engineering at UPES. Apply Today!
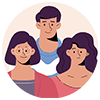
UPES Editorial Team
Written by the UPES Editorial Team
UPES Admission Enquiry
Subscribe to UPES Blogs
Join our community for exclusive stories, insights, and updates
By clicking the "Subscribe" button, I agree and accept the privacy policy of UPES.